Different Types Of Valves And Their Industrial Applications

Valves are simple devices that regulate the flow of liquids and gasses in industries, households etc. Different industrial applications require the use of specific types of valves to meet the precise needs of that particular industry. The making, the structure, and the material used for the valve all depend upon the industrial end-use. In the oil and gas industry, appliances have to deal with high temperature and pressure conditions; hence most valves are made up of stainless steel.
Thus, different types of valves, like globe valves, ball valves, needle valves, butterfly valves, globe valves etc., are manufactured to be of use for several industries.
Different Types Of Valves And Their Usefulness In Industry
Ball Valves
These valves are so named as the fluid flow is controlled by a ball-like structure. A ball which is hollow at the opposite end sits inside a valve body and allows the flow of fluid depending upon the alignment with the open ends of the ball. These valves are open and close by a ninety-degree rotation of the handle. These can be one-piece, two-piece or three-piece ball valves. If one is to understand the uses of each of these, one needs to understand their structural difference.
A 1 piece ball valve, as the name suggests, is a compact one-piece structure where the ball, the body, and the end connections are all a part of a single piece. Hence, in this case, the valve is irreplaceable for any maintenance activity. These structures have no joints; hence they have no chances of leakage within the valve structure. These are used in applications requiring a compact, leak-free, affordable structure.
The difference between a 3 piece ball valve vs 2 piece one lies in the number of pieces that make up the structure. For 2-piece valves, the end pipe connection and the body form one part. A second part that fits into the first part connects the second end of the pipe. Since the structure involves a connection within it, there is a chance of leakage within the valve system. However, these structures have applications in systems where disassembling the system for maintenance and repairs is a necessity.
The three-piece structure has three pieces joined together, and each part is removable. The three parts are the two end caps which connect to the two ends of the pipe and the main body. For the three-piece model, the internal parts are replaceable. Also, these are heavier than 1 or 2-piece ball valves and are more expensive.
Butterfly Valves
In these valves, a disc moves either parallel or perpendicular to the flow of fluid to open or close the valve. The advantage of butterfly valves is that they allow for regulating the exact flow amount, unlike a ball valve where there is a complete shut on and off. Thus, the flow is controlled accordingly if the disc rotation is between the fully perpendicular or parallel position. These valves have tremendous applications in water Treatment plants, the automobile industry and the pharmaceutical industry.
The features of all valves, be they ball valves or butterfly valves, can be improved further by overmolding the body with a material of choice. Injection overmolding is the process of adding a layer of one material over a piece of equipment made up of some other material.
Many ball valves have an overmolding where a PTFE sheet lines the valve structure. Overmolding has several advantages, like giving a more compact structure. Apart from compactness, it can make valves water or corrosion-resistant. PTFE, for instance, is a chemically inert material. It does not react with most industrial acids or solvents. Hence, valves for the food processing industry are often lined with PTFE to reduce food contamination.
Needle Valves
Here a needle-shaped plunger blocks the passage of liquid in a pipe. If the plunger is lifted, the needle does not obstruct the flow. If the plunger is pushed down, it obstructs the flow. These are used for systems which involve slow-flowing fluids and small volumes. These valves are small and sophisticated and help in the precise regulation of flow.
Check Valves
Check valves are needed to prevent the backflow of fluid. Thus once the fluid has passed to the pipe, and the valve closes, then no fluid can flow back. These are useful for systems where upstream apparatus like pumps, etc., must be protected against backflow. These find use in the petroleum refining industry, where they handle viscous fluids.
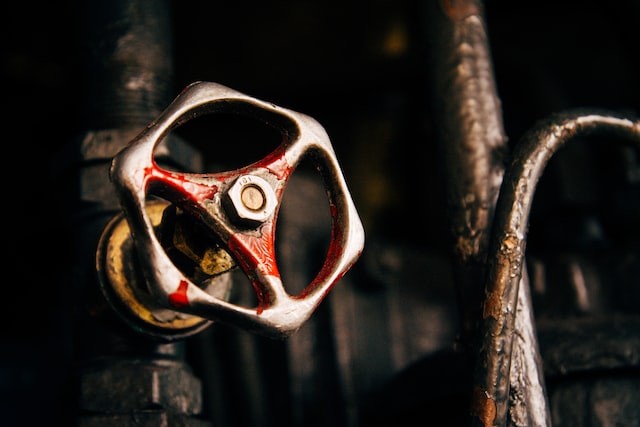
Conclusion
Estimates show that the demand for valves will rise rapidly in the coming years due to the increased pace of industrialization. Hence valve manufacturers are improving the design and structure to cater to the growing needs worldwide. Techniques like overmolding are opening up newer markets for valves where traditional metals like steel or brass have less use.