Fail safe Settings That Prevent Over spraying on a Powder Coating Machine
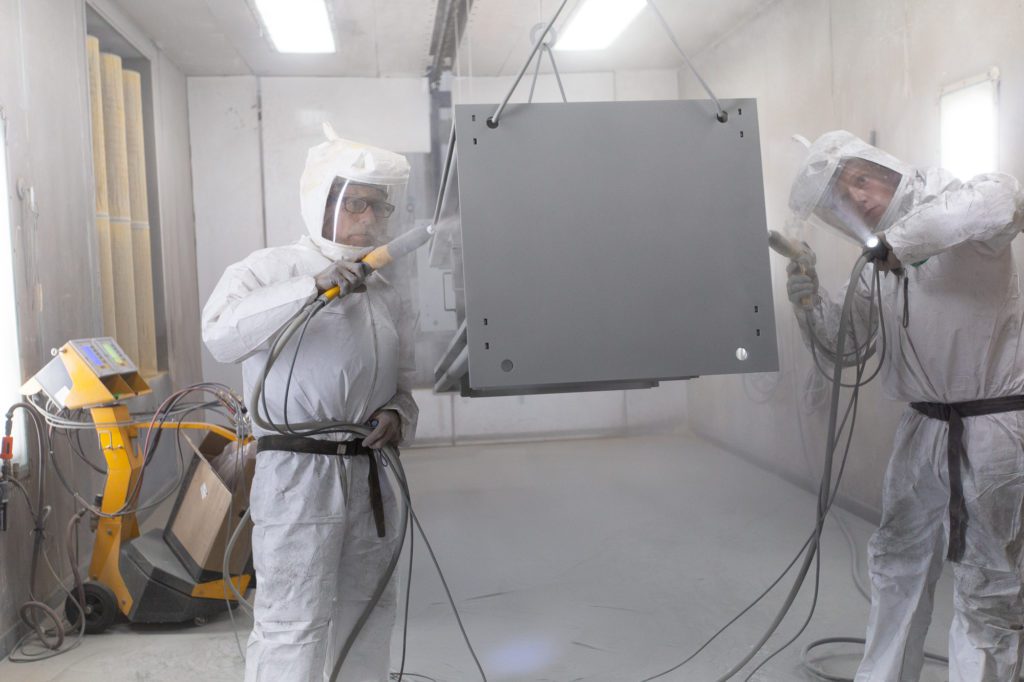
A fine finish doesn’t just happen by chance—it’s often the result of subtle adjustments working behind the scenes. Overspray is one of the most common issues in a coating line, but the right setup can keep it under control without slowing you down. With today’s powder coating machines, built-in safeguards can help operators coat smarter and cleaner.
Electrostatic Voltage Regulation to Limit Powder Waste
Controlling electrostatic voltage is one of the most reliable ways to reduce overspray. In a powder coating machine, voltage charges the powder particles so they cling to the surface of the part. But if the voltage is too high, the charged particles can rebound off the part, leading to waste and uneven coverage. Properly regulating this setting means more powder sticks where it should and less ends up drifting into your spray booth.
Finding the right voltage range depends on the size and shape of the part, the type of powder, and even the part’s grounding. For flat metal parts, a lower voltage might be all you need. Complex parts with corners or deep recesses may require a little more. Dialing in the right numbers allows the powder to wrap efficiently without blasting too much product into the air—and that’s what keeps material usage under control.
Fluidization Pressure Calibration for Uniform Powder Dispersion
Fluidizing the powder is like giving it a gentle lift so it flows smoothly through the hose and gun. If the pressure is off, the powder can clump or surge, making the spray pattern inconsistent. On a powder coating machine, having the fluidization pressure calibrated correctly ensures the powder behaves like a fine mist, not a splatter.
This controlled flow helps coat parts evenly while reducing buildup in the booth. A powder cloud that’s too dense increases the chance of powder bouncing off and landing somewhere it shouldn’t. By adjusting the pressure to match the specific powder type and booth conditions, operators can maintain better control over how the material is applied and where it ends up.
Reasons Nozzle Positioning Significantly Reduces Overspray Risk
Where the nozzle sits in relation to the part makes a bigger difference than most realize. Too far, and powder disperses into thin air before it ever reaches the part. Too close, and you might get thick spots and powder blowback. Positioning the nozzle correctly lets the powder cloud wrap around the part naturally, sticking efficiently and reducing bounce-off.
A well-aligned nozzle should be angled to cover as much surface as possible without direct blast. For parts with grooves or cutouts, adjusting the spray gun’s angle helps get into tight spaces while still preventing stray powder from drifting. Smart nozzle positioning not only improves finish quality, it keeps your workspace cleaner by reducing excess spray that never touches the part.
Powder Flow Rate Adjustments for Consistent Coating Thickness
Flow rate controls how much powder is released through the gun. Too much, and you waste material with layers that are too thick or start to peel. Too little, and coverage becomes patchy. Fine-tuning this setting on a powder coating machine creates a smoother finish with less overspray and no need for rework.
This setting must align with line speed, gun distance, and powder type. For larger parts moving slowly, a higher flow rate makes sense, but it still needs control. With smaller, delicate parts, a slower, gentler application works best. Adjusting flow rate precisely can save both powder and time—and reduce booth cleanup after each job.
Grounding Techniques Ensuring Efficient Powder Transfer
If the part isn’t grounded properly, the powder won’t stick. It’s that simple. Grounding provides the path for electrostatic attraction to work, pulling powder toward the part and locking it in place. Without it, even well-applied powder can drift right past the target.
Using clamps, hooks, or hanging rods with clean metal-to-metal contact ensures the electrical circuit is complete. Routine checks are vital, especially in high-volume shops where coating buildup can interfere with conductivity. Solid grounding isn’t just a best practice—it’s an essential part of reducing overspray and making your powder coating machine work at its best.
Airflow Balance Controls That Minimize Powder Drift
Airflow within the spray booth keeps the environment safe and controls where the powder ends up. If airflow is too strong, powder can be pulled away before it settles on the part. If it’s too weak, particles linger in the air, creating clouds that drift and waste product. Proper airflow balance is key to limiting overspray and getting a clean finish.
Some powder coating machines come with adjustable airflow settings that can be tailored to the size of the booth and type of job. Maintaining consistent airflow ensures that particles head in the right direction and that recovery systems catch excess efficiently. This keeps operators safe, the finish smooth, and waste to a minimum.
Particle Size Matching Settings for Controlled Application
Not all powders are created equal. Finer particles behave differently from coarser ones, and the machine settings must match the characteristics of the powder. Smaller particles can become airborne more easily, while heavier ones may clog or settle unevenly if the flow isn’t set right. Matching settings to particle size ensures an even application and limits the chance of material escaping the part surface. Machines that allow customization for powder type let operators get better results with fewer adjustments mid-job. By aligning air pressure, feed rate, and voltage with particle size, your system delivers powder precisely where it needs to go—reducing both waste and rework. It’s one of those details that feels small but makes a big impact on performance.