Key Functions & Advantages of Owning the Best Plasma Cutter
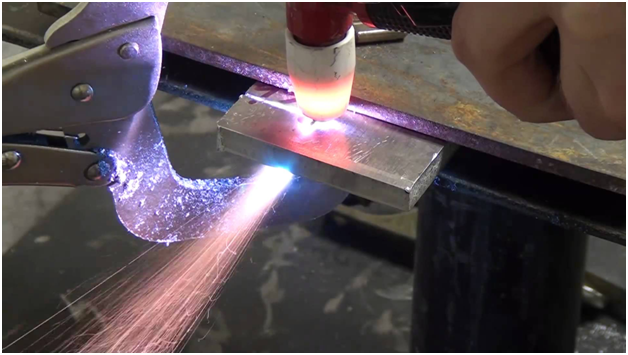
Are you looking to make clean, quick, and smooth metal cuts for your business? Modern industries like automobile and construction depend on the accurate combination of metals and allow- to build the tools. If you have the best plasma cutter for the job, you won’t have to deal with loud grinding, a messy workplace, and inaccurate or rough metal cuts. Metals are extremely strong and durable raw material and because of this, it’s the go-to asset in the production of durable tools.
Specifically designed to cut through the thickest and hardest metals, plasma cutters are best suited for metals. It is an ionized gas torch that heats up and melts electrically conductive material to make a neat and smooth welding output.
How Plasma Cutter Works?
In the plasma cutting mechanism, electrically conductive materials are cut through by means of an accelerated force of hot plasma. In general, the materials that can be precisely cut with a plasma torch are steel, stainless steel, aluminum, brass, copper, and other conductive metals. Plasma cutter is majorly used in manufacturing, automotive repair, and restoration, industrial construction, salvage, and scrapping.
Due to the high speed and precision of the metal cuts at low cost, there is a high demand for welders and plasma cutters from large industrial CNC applications to small hobby companies where the materials are subsequently used for welding metals. It is a plasma cutting conductive gas with a temperature of up to 30,000°C that makes the plasma cutting mechanism and process so reliable.
The process used in plasma cutting and welding is to create an electric channel of heated, electrically ionized gas- i.e. plasma- from the best plasma cutter itself through the metal piece required to be precisely cut, thus forming a finished output at the end of the plasma cutting process. This finished product is obtained by a compressed gas like oxygen, air, inert gas blown to the metal piece at high speed through a focused nozzle. Within the gas, an arc forms between an electrode between the gas nozzle and the metal piece itself. This arc, then ionizes the part of the gas and further creates an electrically conductive plasma network around the weld area. The moment the electric current from the plasma torch flows through the plasma cutter, it produces enough heat to melt through the metal piece. In the meantime, high speed plasma and compressed gas blow the hot molten metal away, separating the final metal piece. As witnessed, plasma cutters produce a very hot cone for cutting metals, they are best for cutting and welding sheets in curved or angled shapes.
Pros of Owning the Best Plasma Cutter
A high-definition plasma cutter has a fast metal cutting speed and it can significantly reduce the amount of heat transferred to the material. Also, it prevents plate warping of thin materials- which mostly occurs when a conventional plasma cutter is used.
When a high definition plasma cutter is used to cut metal up to two inches thick, which is more than a standard size metal, the plasma cutter precisely cuts it as fast as the oxyfuel cutter. In addition, a plasma cutter can cut thin metals up to 12 times faster than any other traditional cutter.
It is one of the best mechanisms to cut any material accurately that conducts electricity. This is because no pre heating is necessary when cutting through a plasma cutter.
Regardless of the work size and the credibility of the welder, one thing is pretty clear: a durable plasma cutter worth the investment.
0 comments