The Incredible Benefits of Vacuum Casting In Product Development
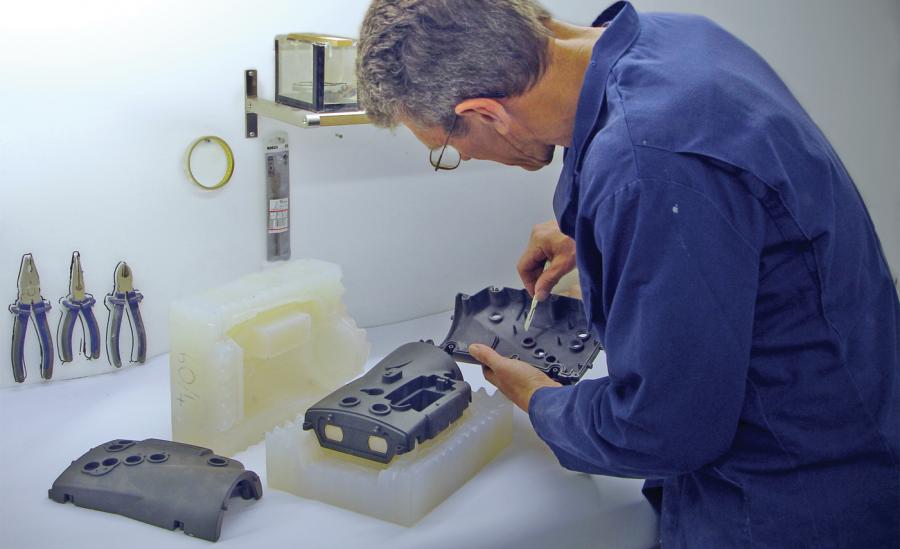
A far more advanced technique in product development is vacuum casting. Its main use is in producing prototypes with far more complicated design and without air entrapments.
This technique involves the use of a vacuum to push the molten material into the flexible molds. It involves two components to produce a product: silicon molds and polyurethanes. Vacuum casting can also bridge production from prototypes to low-volume manufacturing.
Vacuum casting has dominated the prototyping segment of product development for years owing to its speed and accuracy. This method is particularly effective when there is an existing model that can be the basis to replicate.
This article will explore what vacuum casting is, what it has to offer from the perspectives of prototyping and manufacturing, and its pros and cons.
A Brief Background on Vacuum Casting
The vacuum casting technique was first introduced in Europe in the 1960s in the Universities of Dresden and Cottbus of the former German Democratic Republic. It is a technique that uses a combination of well-recognized and conservative technology. Later on, the Japanese have picked up the vacuum casting method and adopted them in automotive parts manufacturing.
In this technique, a flexible mold like rubber is used and the process involves casting the product inside a master model, usually through stereolithography, which can be molded directly from the original part to create a replacement.
This model is produced from silicon rubber and filled with a polyurethane resin and placed in a vacuum. The vacuum process is what removes the air bubbles from the materials with the final product being an exact representation of the master model.
Typically, vacuum casting can create products in small numbers, but it is a quick and more affordable option than 3D Printing. In Europe, vacuum casting is mainly used in research and development to test its industrial capability and quality.
The Benefits of Vacuum Casting
The finished product from vacuum casting has no imperfections and blemishes that you’ll find in other techniques and therefore, all products are identical and flawless. Other than that, here are what manufacturers can benefit from vacuum casting.
- Precision and Quality – These two qualities are the hallmarks of vacuum casting. Its final product has high fidelity to the original. It can also accommodate additional design requirements like threaded inserts and the likes.
- Low-cost of Production – The start-up costs in vacuum casting are relatively low because the molds can be made from cheaper materials.
- Use of Different Materials – One of the functional benefits of vacuum casting is it can use resins that has shock resistant and fire retardant qualities.
- Accommodate Unusual Shapes – Vacuum casting is ideal for creating products with unusual shapes.
- High Repeatability – The mold can be reused countless times.
- Versatility – Vacuum casting can accommodate materials with many different properties. No wonder it is used in the automotive, aerospace, and healthcare industries on their prototyping.
Aside from its accuracy and cost-effectiveness, vacuum casting is also a quick manufacturing process. If you are working on a deadline, it is less prone to error and the best option.
0 comments