Various Types Of Gear-Cutting Tools And How To Use Them
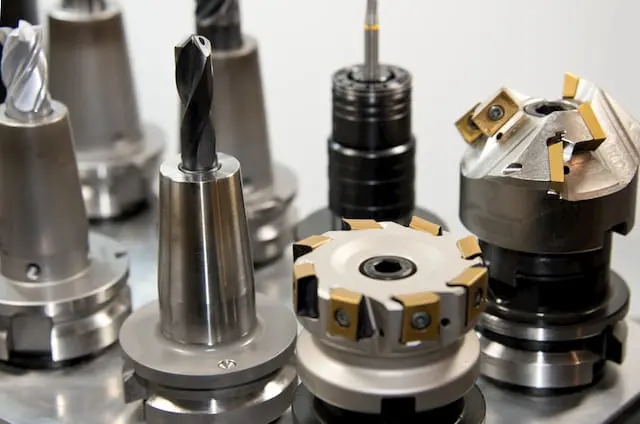
Different processes are involved in gear cutting. Each procedure requires a separate tool. Every tool is made from distinct materials to achieve a successful final product. The material for a particular application depends on the kind of machinery, material that needs to be machined, quality and quantity of production. You can buy these tools as per your need from various gear cutting tool manufacturers in India. As per the materials used, the different types of gear-cutting instruments are
- Carbon tool steel
- High-speed steel tool
- Cemented carbide
- Ceramics tool
- Cubic boron nitride tool
- Diamond tool
- Carbon tool steel
Carbon steel is one of the cheapest gear cutter tool made of metal used for mild-speed machine operations. These simple Carbon tools have 0.6-1.5% Carbon and small quantities of manganese and silicon. Metals like vanadium and chromium alter the grain size and hardness. High-quality Carbon steels are impervious to abrasions and can maintain a sharp cutting edge. Carbon tool steel has substantial machinability. It loses hardness rapidly at temperatures around 250 degrees Celsius and hence cannot work in high-temperature settings.
Carbon steel equipment is used in milling tools, turning and forming tools, twist drills, and soft materials like aluminium, magnesium, brass, etc.
High-speed steel
It is a high Carbon steel with significant amounts of alloys like molybdenum, tungsten, chromium, etc. These alloys improve the tool’s hardness, durability and resistance. It imparts higher metal removal strength. The equipment loses hardness at 650 degrees Celsius, and you can use a coolant to increase the shelf life. HSS can be used many times by resharpening or performing some surface treatment.
Cemented carbide tool
This equipment is produced by the powder metallurgy method. It is made of tungsten, tantalum and titanium carbide with cobalt as a binding agent. These tools are hard and can withstand high-speed cutting operations. They don’t lose hardness up to 1000 degree Celsius. Low cobalt is for finishing, whereas high cobalt helps to carve a rough cut.
Ceramics
The most common ceramic composites are aluminium oxide and silicon nitride. Ceramic instruments are inert and resistant to corrosion. They have better compressive strength and are stable even at temperatures of 1800 degrees Celsius. They are faster than HSS and provide an exceptional surface finish. The friction between the chip and tool face is low. So, no coolant agent is required.
Cubic boron nitride
Cubic boron nitride is the second solid material used in hand machines. They provide high resistance to abrasions and serve as an abrasive in grinding wheels.
Diamond
Diamond is one of the sturdiest materials, and its cost is no secret. Diamond has a very high melting point and thermal conductivity. It offers superb abrasion resistance, low thermal expansion and friction coefficient. It is used to machine hard materials like carbide, nitride, glass, etc. These tools give an excellent surface finish and dimensional precision but are not advised for machining steel.
These are the tools used for gear cutting tools that produce brilliant and high-quality gears required for various types of machinery.