The Five Most Important Tips for Conducting an Effective Manufacturing Process Audit
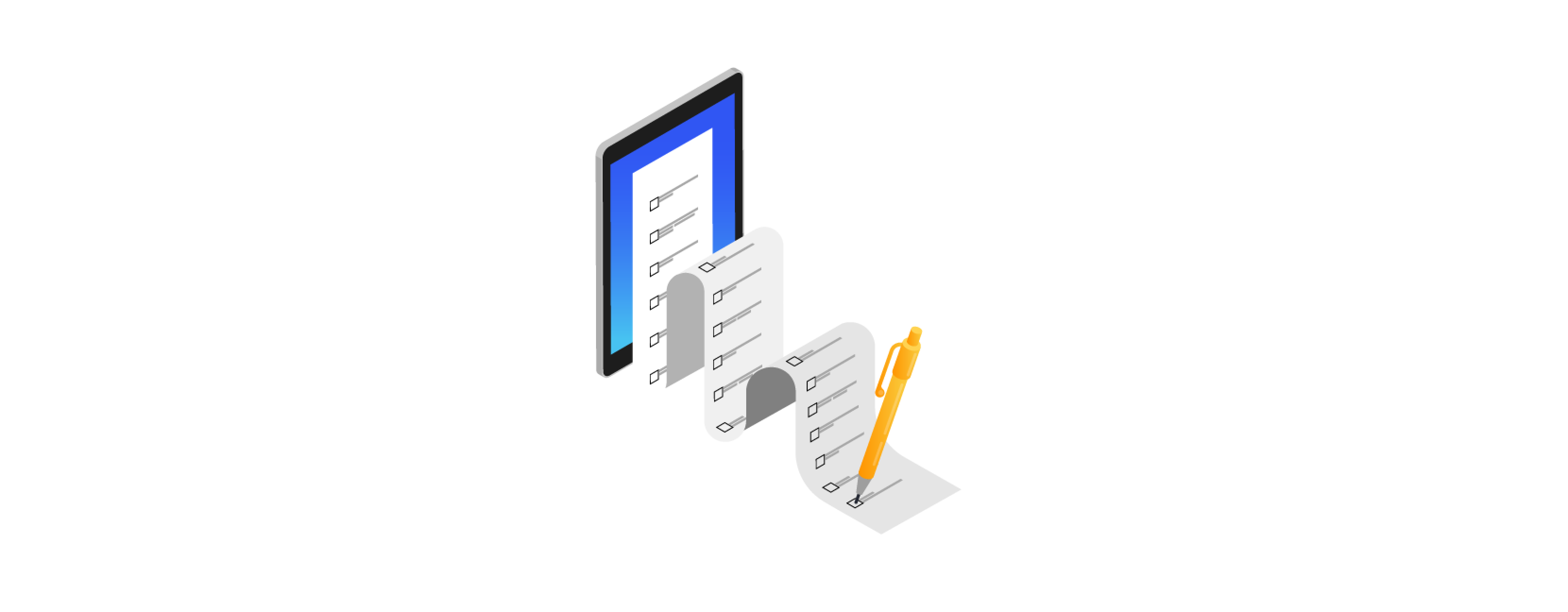
When you’re the head of an organization, it’s your job to keep everything running smoothly. That means you need to make sure that every department within your company is working in top form, and this includes the manufacturing process as well.
Conducting an effective manufacturing process audit can help you uncover potential weaknesses that could cause problems down the road, allowing you to remedy them before they get out of hand. This article will introduce you to five of the most important tips to keep in mind when conducting an effective manufacturing process audit at your company.
Understand the Business
Successful audits start with a clear understanding of the business goals. You’ll need to become familiar with the company and its mission, as well as identify areas where manufacturing could be streamlined or improved. Additionally, you should understand how each production process is related to the business strategy; if it doesn’t fit into that plan, you’ll want to determine whether it can be incorporated in some way.
Finally, be sure you fully understand all relevant safety regulations and standards. These are critical when auditing a manufacturing process because they will help ensure production processes remain safe and effective; violations may pose risks to customers or the environment and must therefore be identified so they can be addressed and resolved quickly before serious problems occur.
Know the Audience
When writing any kind of audit, you need to know your audience and the context of the situation. An effective manufacturing process audit should be both actionable and easy to understand, which means avoiding needless jargon or unnecessary technical details.
The three main parties involved in an effective manufacturing process audit are the auditors themselves, who conduct the audit; management, who set the vision and lead change; and the operators, whose job it is to execute that vision.
Auditors (and management) should therefore prioritize their report with operator-friendly language that makes recommendations easy to act on. Operators can then convey those findings more easily to management, ensuring buy-in from those at all levels of a company.
Analyze Data
You’ll want to take a hard look at where you stand. How do your results compare to those of your competitors? In what areas are you weak, and how can you improve? To evaluate your processes effectively, be sure to analyze data precisely.
According to Caliper Corporation, analyzing each variable in conjunction with one another is important in order to get as complete a picture as possible. For example, if you’re looking at yield rates, compare initial production rates with scrap rates and production failures after post-production inspection. As Dave Bostwick of Reticle Vision Systems says: Yield analysis allows us to maximize our throughput while maintaining quality control.
Explore Possibilities
The purpose of a manufacturing process audit is to evaluate how well your team is producing and what areas can be improved. Unfortunately, most people get stuck on one end of the spectrum: they either want to measure effectiveness or improve it by making changes. In reality, you should do both. The best way to get started is by exploring all possibilities so that you have a strong baseline from which to work.
Make sure you’re using production data, but also look at company financials and customer satisfaction levels too; these numbers will help paint a picture of what is working and what isn’t in manufacturing processes today. Also, factor in environmental concerns as part of your analysis – there are many variables outside manufacturing that need to be considered when deciding where changes need to be made within a factory.
Prioritize Problems
Look at each problem and rank it from 1 to 5. 1 = This is a huge problem; 2 = This is something that needs to be changed; 3 = I don’t like it but can live with it; 4 = No big deal, no action required. Knowing which problems need to be fixed first is key. Without prioritizing, you may spend too much time on something that isn’t that important.
At the same time, you may overlook a major issue because it doesn’t appear to be a high priority. The former will cost your company money while creating internal strife (the latter will also do both).
Conclusion
Quality Control Inspection service is commonly needed by manufacturers, to maintain their production processes and product quality. Here are five tips that will help you get more out of your next inspection or audit. Consider using all five when conducting a manufacturing process audit, as part of the Quality Control Inspection service, in your own business. You’ll be able to efficiently uncover issues and opportunities that can ultimately save time and money while helping you continue to build a better business. Best of luck!