The Importance of Conducting an SA8000 Audit of Your Suppliers
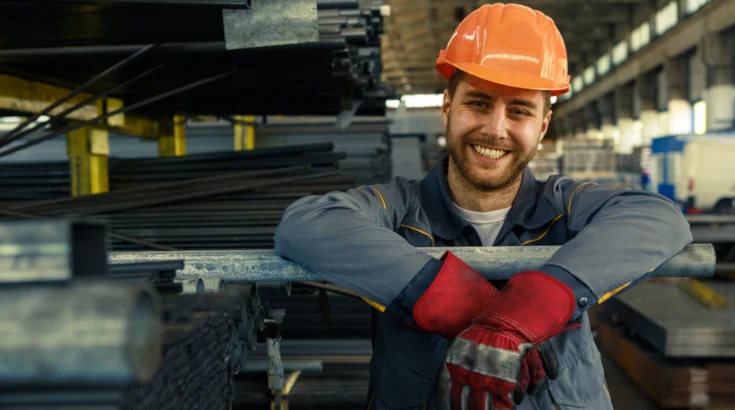
Any enterprise’s success is fundamentally reliant on the caliber of their suppliers and the goods they offer. To guarantee your providers comply with the criteria that you establish, it is vital to administer an SA8000 audit. SA8000 is an internationally accepted certification that provides a comprehensive examination of a supplier’s agreement to social and labor regulations. By conducting an SA8000 audit, businesses can guarantee their suppliers operate in a socially conscientious way and provide quality items. In this article, we will explain the significance of executing an SA8000 audit of your suppliers.
What Is SA8000?
SA8000 is a groundbreaking, global certification standard which is voluntarily implemented and externally monitored. Developed in 1997 by Social Accountability International, this auditable standard aims to improve the working conditions of factories and organizations across the world by addressing areas such as child labor, forced labor, health and safety, freedom of association, discrimination, wages and benefits, working hours, and disciplinary practices. Nowadays, SA8000 is used by more than 5,000 companies in over 80 countries, providing a platform for ensuring the wellbeing of workers and upholding ethical practices. This has enabled corporations to illustrate their corporate social responsibility, enhance customer relationships, and establish ethical supply chains.
The Benefits of Conducting an SA8000 Audit
The implementation of an SA8000 audit for suppliers can provide numerous benefits that positively influence labor practices on a global scale. This comprehensive set of standards, which are intended to bolster the security and fairness of worker rights, help to enhance conditions such as health, safety, hours and wages. The primary advantages of such an audit include:
1. Improved Workplace Standards: Executing an SA8000 audit helps to ensure that suppliers are either meeting or exceeding expectations in terms of worker safety, working hours, and wages, ultimately leading to better overall conditions.
2. Accountability: These audits ensure that suppliers are held accountable for their practices and must adhere to the aforementioned standards.
3. Strengthened Relationships: It’s possible to construct trust between an organization and its suppliers through these audits, leading to better collaboration between parties.
4. Improved Reputation: A successful SA8000 audit signals to the public that the organization is committed to ensuring ethical practices throughout their supply chain. This is a great way to boost the public image of the organization and can potentially give them a competitive advantage.
By providing organizations with the tools to monitor the safety and ethicality of their supplier labor practices, an SA8000 audit ultimately helps to build a culture of trust, transparency, and accountability that has tangible effects on all stakeholders.
How to Conduct an SA8000 Audit
An SA8000 audit of a supplier is an essential step to make sure that international labor standards are met. SA8000 is a certified international accountability standard, and an auditor that is approved by an organization should be brought in for an assessment.
For starters, the supplier must present the auditor with the pertinent management system documents. This can involve labor contracts, employee records, health and safety guidelines, and work hours. As part of the evaluation, the auditor will speak with the staff, management included, to ensure that the established protocols and practices are being applied.
Afterward, the auditor will investigate the supplier’s performance against the eight core requirements of SA8000: child labor, forced labor, health and safety, freedom of association, disciplinary practices, and working hours. Further areas of the SA8000 standard, such as training and complaint mechanisms, may also be considered. If the audit uncovers any discrepancies, the supplier should resolve the issue and demonstrate that corrective action was taken.
Once the audit is done, the auditor will generate a report that contains their findings and proposed actions. For continued adherence to SA8000 standards, the supplier must follow the advice provided in the report.
What to Do if Your Supplier Does Not Meet the SA8000 Standards
To tackle the shortcomings noted in the SA8000 audit, it is vital to get a handle on the magnitude of the issue. The audit will have detailed any areas where the supplier failed to adhere to the criteria and supply counsel for how to correct them. If the trouble is more significant, you might need to consult an external expert for further evaluation and resolution.
After you have ascertained the reach of the trouble, the next step is to implement remedial measures. This may consist of retraining workers or updating operations, or, if the trouble is serious, even ceasing your relationship with the supplier.
Lastly, vigilantly track development. Make sure corrective measures are quickly and effectively enforced. Additionally, ensure you perform follow-up audits frequently to ascertain if the supplier meets the SA8000 standards. This will aid you in uncovering any further problems and guarantee that the supplier carries on meeting the necessary criteria in the future.