The Role of Quantum Metrology in Advancing Semiconductor Technologies
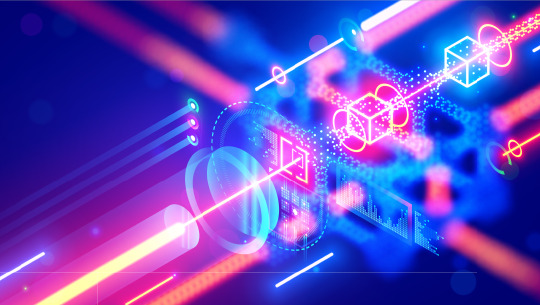
As semiconductor technology continues to push the boundaries of miniaturization and performance, the demand for more precise measurement techniques has never been greater. Traditional metrology methods, while effective for previous generations of chips, struggle to provide the accuracy required for atomic-scale manufacturing. Erik Hosler, an expert in advanced semiconductor metrology, recognizes that quantum-based measurement techniques are revolutionizing the industry by setting new standards for precision and reliability in semiconductor fabrication.
Why Quantum Metrology is Essential for Semiconductor Manufacturing
Semiconductor devices are now being manufactured at the atomic level, where even the smallest variations in material composition, layer thickness, or electrical properties can impact performance. Traditional metrology tools, which rely on optical and X-ray-based methods, face limitations when measuring structures at such an extreme scale. As chipmakers transition to technologies like gate-all-around (GAA) transistors, 3D stacking and quantum computing architectures, the need for ultra-precise measurement techniques becomes critical.
Quantum metrology leverages the unique properties of quantum mechanics, such as entanglement and superposition, to achieve unprecedented levels of measurement accuracy. These principles allow for the detection of sub-nanometer defects and atomic-level material variations that conventional tools might miss. By harnessing quantum phenomena, semiconductor manufacturers can ensure greater consistency and higher yields in advanced chip production.
Quantum Sensors: Unlocking New Levels of Precision
One of the most promising innovations in quantum metrology is the development of quantum sensors, which provide far greater sensitivity than traditional semiconductor inspection tools. These sensors can detect minute changes in magnetic fields, temperature and electrical resistance, enabling fabs to measure materials and device structures with near-perfect accuracy.
For example, diamond nitrogen-vacancy (NV) centers are being used to visualize nanoscale defects in semiconductor wafers. These quantum-based sensors provide high-resolution, non-destructive imaging, allowing manufacturers to analyze material properties in real time and optimize production processes accordingly.
Free-Electron Lasers and Quantum Light Sources
Next-generation semiconductor metrology is also benefiting from the integration of quantum-based light sources, such as free-electron lasers (FELs). These high-intensity, tunable lasers provide sharper imaging and deeper penetration, making them ideal for detecting hidden defects within complex, multi-layer semiconductor structures.
Erik Hosler highlights, “Free-electron lasers will revolutionize defect detection by offering unprecedented accuracy at the sub-nanometer scale.” By incorporating FELs into metrology systems, fabs can significantly improve their ability to inspect advanced semiconductor designs, ensuring higher quality control and reducing material waste.
The Future of Quantum Metrology in Semiconductors
As semiconductor manufacturing moves further into the Angstrom era, quantum metrology will play a crucial role in maintaining precision, efficiency and reliability. The combination of quantum sensors, advanced light sources and AI-driven data analysis is transforming how fabs approach measurement and quality control.
Looking ahead, quantum metrology will be instrumental in developing next-generation processors, quantum computing devices and ultra-low-power semiconductors. With these advancements, the industry is poised to achieve breakthroughs in performance while ensuring the highest standards of manufacturing accuracy.
By integrating quantum-based measurement techniques into semiconductor fabrication, manufacturers are not only meeting today’s challenges but also paving the way for the next evolution in chip technology.